What Manufacturers Need to Know About the Global Supply Chain Disruptions
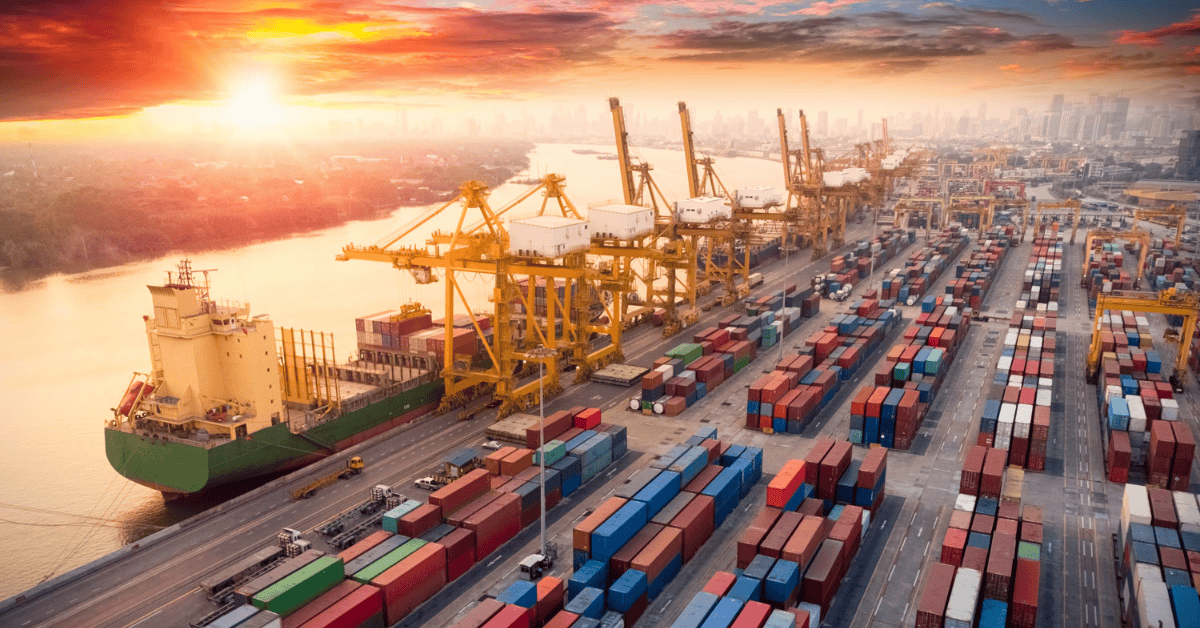
It’s no secret that 2022 has seen its share of challenges for manufacturing operations, and Dallas manufacturers are not immune to these global struggles.
A recent KPMG report found that 67% of CEOs will increase investment in detecting disruptions to their supply chains and will look to process innovation to help alleviate threats to global business operations.
Global manufacturers need to become more flexible and resilient to meet the challenges of the current business environment. The New York Fed states, “The [Global Supply Chain Pressure Index]’s year-to-date movements suggest that although global supply chain pressures have been decreasing, they remain at historically high levels.” (August 2022)
In fact, the Fed’s estimated pressures on the global supply chain in 2022 are higher than all reported rates since the Fed started this index in 1997 and even higher than the pressures experienced in 2020 during the global pandemic shutdown.
The Issues:
Logistics Challenges
Labor shortages and workforce issues have made staffing warehouses and production lines more challenging than ever. Disruptions to transportation caused by port shutdowns, environmental disasters, labor union strikes and geopolitical conflict are adding uncertainty on a day-to-day basis. And experts expect the looming energy crisis in Europe to exacerbate these issues into the winter months. KPMG cited Logistics Challenges as the No. 1 issue for manufacturers in 2022.
Materials Shortages
As if these logistics challenges weren’t enough, manufacturers continue to face unprecedented material shortages. Even those CEOs who have mastered their supply chain and eliminated their risk on that front still have to contend with an ever-changing landscape of raw material availability.
Commodity Pricing
Rapid inflation is driving up the costs of commodities and adding uncertainty to financial forecasting. As raw materials prices rise, manufacturers may want to hold back on stockpiling inventory, but others may want to increase supply as a hedge against rising prices. This kind of unpredictability challenges procurement professionals and causes misalignment between the cost of goods and category pricing.
Consumer Demand
As inflation rises, consumer demand becomes even more unpredictable. Wild fluctuations in consumer confidence and rapidly decreasing buying power make it harder than ever to forecast consumer demand for manufactured products.
What Can Manufacturers Do?
Increase Visibility into Supply Chain and Spending
As difficult as it is to plan for an unpredictable future, a lack of visibility into where your raw materials are coming from and how much they cost can be a death knell. You can’t know what you can’t see, and companies are increasingly turning to new technologies to assist with planning, tracking, tracing and responding to issues in real-time.
Leverage Third-Party Relationships
Third-party relationships can be a critical part of your growth strategy. They provide variable cost solutions rather than long-term fixed overheads, and they can allow you to pace investment in your operation’s growth while gaining immediate expertise.
Procure “Release Valve” Solutions
Take the time to source vendors that can help provide a release valve for unpredictable elements of your business. Select a Partner partner with a third-party carrier that can pick up routes when you have unusually high transportation needs. Find warehouses that can accept delivery ofon materials and store them until they are needed. Lining up relationships now can help when you are in a pinch and need to respond to a situation before it becomes a crisis.
How a 3PL Can Ease the Tension
All the issues bearing down on manufacturers today call for innovative solutions. Third-party logistics (3PL) providers like Armstrong have experts on hand to help you plan for unpredictable supply and demand.
Transportation issues can delay offloading of finished goods, leaving you with the need to find a place to store that product until it can be shipped. Or perhaps you need to increase your volume of packaging materials to meet a new minimum order threshold imposed by a squeezed supplier. Or maybe you need to stockpile raw materials that are becoming hard to procure or are increasing in cost.
An offsite warehousing and storage solution can help relieve pressure on manufacturers by storing a variety of materials, including raw materials, packaging materials and finished goods ready to ship to wholesalers or end consumers.
Contact an Armstrong representative today to see how your operation can benefit from our innovative business solutions. Get started by calling 972.242.0511 or requesting a free quote online.