Nearshoring vs. Reshoring: Choosing the Right Strategy to Fortify Your Supply Chain
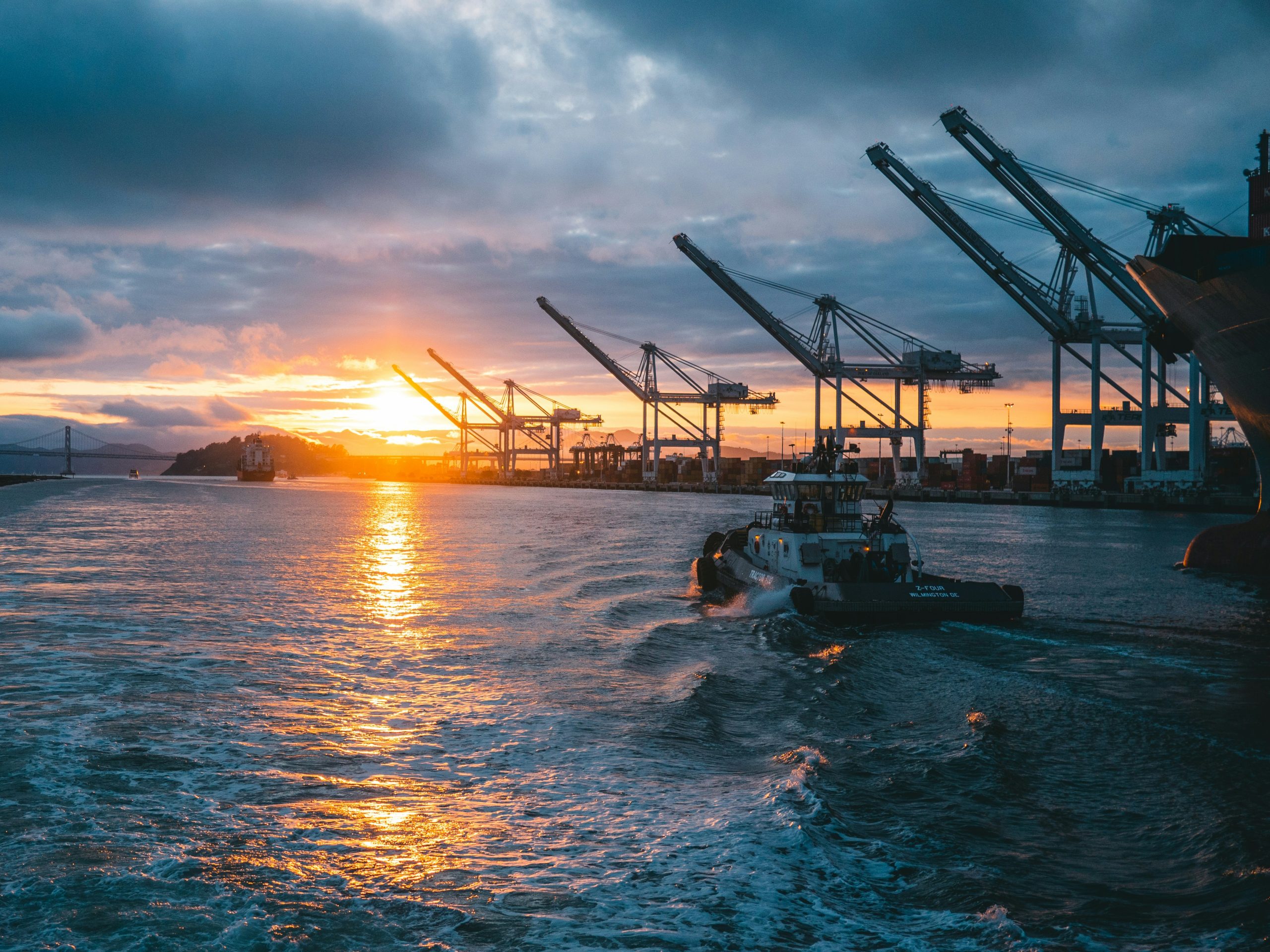
In recent years, we’ve witnessed how global events have caused major disruptions in the supply chain. This has led businesses worldwide to reconsider their offshore manufacturing strategies. As a result, the terms reshoring and nearshoring have become central concepts in building more resilient supply chain solutions.
What is Reshoring?
Reshoring is the process of bringing manufacturing and service jobs back to a company’s home country after they were previously moved overseas. This is the opposite of offshoring, where companies relocate production facilities and operations to other countries, typically seeking to reduce costs and regulatory burdens.
Origins of Reshoring
While the concept of reshoring has existed for some time, it gained significant momentum in the early 2000s. Several factors contributed to its rise:
- Rising Offshore Costs: As wages and operating expenses rose in traditionally low cost countries like China and Mexico, the cost advantages of offshoring began to diminish.
- Quality Concerns: Companies faced potential risks surrounding product quality, consistency, and communication with distant suppliers.
- Supply Chain Vulnerabilities: Global events including natural disasters and the early waves of the COVID-19 pandemic exposed the challenges of relying on complex supply chains spanning vast distances.
- Shifting Consumer Preferences: A growing consumer focus on ethically sourced products and local job creation encouraged considering reshoring.
How Reshoring Is Used in Supply Chains Today
Today, reshoring is seen as a key strategy for organizations aiming to:
- Enhance Supply Chain Resiliency: By reducing dependence on long, complex global supply chains, reshoring makes businesses less vulnerable to disruptions.
- Boost Domestic Manufacturing Operations: Reshoring contributes to revitalizing the domestic production sector and creating jobs within the home country.
- Improve Responsiveness: A production process closer to the end market allows organizations to react more quickly to changing customer demands and market fluctuations.
- Ensure Quality Control: Organizations gain greater oversight and control over manufacturing operations and the quality of finished products when management is closer to home.
- Protect Intellectual Property (IP): Reshoring can help to mitigate the risk of IP theft that may be higher in certain offshore locations.
Industries Leading in Reshoring:
Reshoring is embraced across various industries, including:
- Manufacturing: Companies in sectors like electronics, automotive, textiles, and medical equipment are moving production to address supply chain challenges and improving control.
- Technology: Technological advancements like automation and robotics are making reshoring more feasible and cost-competitive, even in the technology sector.
- Service Industries: Some companies are also reshoring customer service, IT support, and other service-oriented functions back to their native country.
What is Nearshoring?
Nearshoring involves relocating business operations to a nearby country, usually one sharing a border or within the same region. In contrast to offshoring, which focuses on finding the lowest cost locations globally, nearshoring prioritizes proximity, cultural similarities, and time-zone alignment.
Origins of Nearshoring
The concept of nearshoring emerged in response to the challenges of traditional offshoring. As companies were experiencing rising expenses, communication issues, logistical problems, and other associated risks with distant partners, nearshoring aimed to strike a balance between cost savings and geographic convenience.
How Nearshoring Is Used in Supply Chains Today
Nearshoring offers many benefits and has been adopted for various reasons across different sectors:
- Mitigating Risk: Nearshoring helps enterprises diversify their supply chains and reduce their dependence on single, far-off manufacturing locations.
- Cost Optimization: While not as inexpensive as some distant offshoring locations, nearshoring still offers significant cost savings in labor, shipment, and overhead compared to local management.
- Greater Control and Proximity: The shorter distance allows for closer supervision of production processes and skilled workers, faster product iterations, and better communication with nearshore supply chain partners.
- Similar Time Zones: This facilitates real-time collaboration and coordination between teams based in the company’s nation and the nearshore location.
- Cultural Similarities: Operating in a nation within the same region often means a better understanding of business practices, regulations, and consumer preferences.
Examples of Nearshoring Destinations
Facing a local warehouse shortage and in the process of searching for nearby locations, the choice of popular nearby destinations varies depending on the company’s home country.
For example:
- For US companies: Mexico, Central America, and parts of the Caribbean offer advantages in logistics, labor expenses, and trade agreements.
- For European companies: Eastern Europe and North Africa provide skilled workers and convenient proximity.
Industries Utilizing Nearshoring:
- Manufacturing: Industries ranging from automotive and electronics to apparel and furniture leverage nearshoring for supply chain flexibility and competitive costs.
- Software Development: Many companies nearshore software development projects to tap into the tech talent pool of neighboring nations while maintaining ease of collaboration
- Customer Support: Companies nearshore customer service and call centers to benefit from lower labor costs and find multilingual resources.
The Driving Forces Behind Reshoring and Nearshoring
Among the several factors that make reshoring and nearshoring compelling prospects for manufacturing companies, you may find:
- Global Supply Chain Disruptions:The COVID-19 pandemic has exposed the challenges manufacturers face dealing with the fragility of global supply chains.Port closures, factory shutdowns, and shipment bottlenecks massively disrupted product flows. These supply chain disruptions led to severe delays, stockouts, and skyrocketing costs. Thereby, companies realized the inherent risks in overly long, complex supply chains, fueling the interest in moving manufacturing operations closer to gain more control and build resilience in their production process.
- Rising Logistics Costs:Transportation costs have increased due to multiple factors, including fuel price surges, container shortages, and port congestion.This erodes the potential cost savings that were once the main driver of offshore manufacturing. Reshoring and nearshoring reduce transportation expenses and partially mitigate the impact of rising logistics expenses.
- Geopolitical Tensions:Shifting trade policies, tariffs, and geopolitical instability create a volatile environment for businesses that rely heavily on suppliers in distant countries.The potential for sudden disruptions due to political factors pushes companies towards reshoring or nearshoring to reduce risk and secure their supply chains from unpredictable global events.
- Focus on Sustainability:Consumers are increasingly conscious of the environmental impact of products and demand greater transparency.Long-distance movement associated with offshore manufacturing contributes significantly to a company’s carbon footprint. Reshoring and nearshoring can shorten transportation routes and potentially reduce emissions, appealing to sustainability-minded consumers and helping companies meet environmental goals.
Weighing the Benefits of Reshoring and Nearshoring
Both reshoring and nearshoring offer ways to build more resilient supply chains and mitigate risks, including:
- Increased Supply Chain Resilience: Reducing reliance on a distant supplier enhances control, adaptability, and response times in the face of disruptions.
- Shorter Lead Times: Moving manufacturing operations closer to the end market speeds up product delivery and improves responsiveness to demand fluctuations.
- Quality Assurance: Reshoring and nearshoring can facilitate better oversight of product quality and compliance.
- Greater Agility: Businesses gain flexibility to modify production schedules and pivot quickly, which is essential in volatile markets.
- Intellectual Property Protection: There is a reduced risk of intellectual property theft in countries closer to home or with stronger legal systems.
While nearshoring and reshoring offer undeniable benefits, it’s essential for your company to be fully aware of the potential challenges associated with both supply chain strategies. Here’s a breakdown of the key concerns:
Challenges of Nearshoring
- Higher Costs: While nearshoring typically offers cost savings compared to domestic operations, labor costs and operating expenses may still be higher than in more distant offshoring locations. This is why it’s key to carefully assess if these expenses align with their budgets and the potential benefits.
- Limited Infrastructure: Some nearshoring destinations may not have the fully developed infrastructure that can support large-scale manufacturing. Businesses need to factor in potential investments required for infrastructure improvements or find locations with adequate facilities.
- Skilled Labor Shortages: Depending on the country, finding skilled workforce with the necessary technical expertise might be a challenge. It’s crucial to conduct thorough market assessments and organizations may need to invest in upskilling and training programs.
- Cultural and Language Differences: Even though nearshoring often involves countries within the same region, there can still be cultural and language barriers that affect communication and collaboration.
- Intellectual Property (IP) Risks: While generally lower than in some offshore locations, the risk of IP theft or inadequate protection still exists in nearshore countries. Companies need to take additional precautions and consider contractual safeguards.
Challenges of Reshoring
- Substantially Higher Costs: Labor costs, along with various operational expenses, tend to be significantly higher in a company’s nation compared to most offshoring or nearshoring locations. This is one of the primary challenges to weigh against potential benefits.
- Availability of Skilled Labor: Depending on the industry, reshoring may be difficult due to a shortage of workers with the specific skills and experience needed for the company’s manufacturing processes.
- Re-establishing Supply Chains: Shifting operations back home often requires building new supply chains and finding domestic suppliers, which can be a lengthy and complex process.
- Transitional Period: Reshoring is usually a gradual process. Disruption to existing supply chains and potential delays during the transition period need to be carefully managed.
- Potential Consumer Pushback: In some cases, consumers may have negative perceptions about the increased cost of domestically manufactured goods, especially if they were used to lower costs associated with offshore production.
Important Considerations When Choosing the Right Strategy:
The severity of these challenges varies depending on the specific industry, company size, and the selected nearshore or reshore location. It’s crucial for companies to conduct thorough research and consider the following:
- Total Cost of Ownership: Analyze not just individual costs, but the total cost of ownership, including aspects like transportation, inventory holding, risk mitigation, and potential lost sales due to disruptions.
- Long-term Strategy: Evaluate whether nearshoring or reshoring aligns with the company’s overall strategic objectives and its commitment to creating a sustainable and agile supply chain.
There’s no one-size-fits-all answer when it comes to where to open a company’s warehouse or invest in new facilities. The best strategy dependes on a company’s unique circumstances and objectives. Here’s a framework to help your company make an informed decision:
1. Thorough Supply Chain Assessment
- Identify Vulnerabilities: Analyze your current supply chain and pinpoint areas of weakness. For example, where have you experienced disruptions, delays, quality problems, or unexpected costs?
- Quantify Risks: Assess the potential financial impact of continued supply chain disruptions. Make sure your report notes lost sales, penalties, or damage to your brand reputation.
- Map Your Priorities: What are the most important goals you want to achieve with a shift toward reshoring or nearshoring? Is it minimizing risk, maximizing speed, controlling expenses, or a combination of factors?
2. Evaluate Reshoring vs. Nearshoring Options
- Cost Analysis: Conduct a detailed cost comparison. Consider not just labor and material expenses, but also logistics, overhead, tariffs, and potential tax incentives associated with each option.
- Availability of Skilled Labor: Research the availability of talent pools with the required skills, both in your country (for reshoring) and in potential nearshore destinations.
- Proximity: Determine how important close proximity and time-zone alignment are for your operations. For example, does your business require frequent on-site interactions or quick turnaround times?
- IP Protection: Assess the intellectual property laws and enforcement in your home country and in potential nearshore locations.
- Sustainability Impact: Consider how different options might reduce or change your carbon footprint based on transportation distances and energy sources.
3. Explore Potential Locations
- Analyze Home Country Options: Evaluate the domestic infrastructure, workforce availability, and potential incentives in different regions within your country.
- Research Nearshore Destinations: Investigate specific nearshoring destinations that offer favorable labor costs, trade agreements, skilled workforce, and political stability.
4. Consider a Phased Approach to Avoid Supply Chain Disruptions
- Pilot Projects: Instead of fundamentally changing your entire supply chain, consider testing nearshoring or reshoring on a smaller scale. Start with a specific product line or a less complex part of your operation.
- Hybrid Model: Sometimes a hybrid approach, with a mix of reshoring, nearshoring, and strategically maintaining some offshore partnerships, might offer the best balance of resilience and cost optimization.
Additional Components to Consider:
- Long-Term Outlook: Consider the company’s growth trajectory and potential future needs. Will reshoring or nearshoring accommodate anticipated growth, increased demand, and scalability?
- Technology Integration: Assess the role of new technologies in making reshoring or nearshoring more feasible. Investments in automation or robotics might offset higher labor costs.
Seeking Expert Advice:
Consulting with supply chain experts, trade organizations, or government agencies that specialize in reshoring or nearshoring can provide valuable insights and guidance throughout the decision process.
Armstrong has over three generations of experience implementing supply chain solutions in a variety of industries, and we have the expertise, technology, and resources needed to ensure your success in today’s complex and dynamic supply chain environment.
Armstrong offers supply chain analysis and support for your business, including ways to optimize your network, improve services, identify and implement alternative strategies, and reduce costs. Armstrong’s logistics experts provide supply chain solutions that cover everything from production, transportation, distribution, engineering services, and more—all designed with a deep knowledge of your specific business in mind.
Whether you are looking for ways to streamline a few processes, implement nearshoring or reshoring to improve operations, or completely overhauling your supply chain network, Armstrong has the expertise and resources to provide data-driven analysis and customized solutions to move your business forward.
Reshoring and Nearshoring Success Tips
Planning Phase
- Set Clear Objectives: Define the specific reasons for relocating (e.g., reduced risk, improved speed-to-market, cost savings, etc.) and set measurable targets for success.
- Thorough Cost Analysis: Conduct a comprehensive analysis beyond just labor costs. Include aspects like transportation, logistics, tariffs, duties, taxes, potential incentives, and the real cost of supply chain disruptions in your calculations.
- Select the Right Location: Carefully evaluate locations based on labor costs, skills availability, infrastructure, political stability, IP protection, and alignment with your objectives.
- Develop a Detailed Transition Plan: Create a timeline with milestones covering ramp-down of old facilities, ramp-up in the new location, supply chain adjustments, workforce changes, and mitigating potential disruptions.
- Communication and Stakeholder Buy-in: Secure support and alignment with internal stakeholders and communicate the plan clearly to suppliers, customers, and employees.
Implementation Phase
- Partner Selection: Choose reliable suppliers and logistics partners in your target location. Due diligence is vital; consider on-site visits and background checks.
- Establish a Local Presence: Depending on the scale of operations, set up a legal entity or liaison office to navigate the regulatory framework and cultural nuances of the new location.
- Invest in Training: Provide necessary training and onboarding for employees in the new location to ensure alignment with your company’s quality standards and processes.
- Knowledge Transfer: Implement a robust plan for transferring knowledge and expertise from existing operations to the new site to ensure a smooth transition.
- Technology Integration: Leverage technology platforms to streamline communication, data sharing, and visibility across your supply chain.
Monitoring and Optimization
- Set KPI Tracking: Establish key performance indicators (KPIs) to measure the success of your transition. Track factors like cost savings, lead times, quality metrics, and customer satisfaction.
- Continuous Improvement: Regularly review your processes, identify areas for optimization, and address any bottlenecks or challenges that might arise.
- Maintain Flexibility: Remain adaptable as supply chains and market conditions are dynamic. Be prepared to adjust your approach for long-term resilience and competitiveness.
Tips for Success
- Start Small: Consider a pilot project to test a nearshore or reshore strategy with limited products or operations before fully committing to a larger transition.
- Phased Approach: Implement reshoring or nearshoring gradually to minimize disruptions and allow for adaptation along the way.
- Strong Relationships: Foster collaborative partnerships with suppliers and stakeholders in the new location.
- Cultural Awareness: Invest in cultural training for your team to bridge gaps and facilitate effective communication and teamwork.
Remember: A successful transition requires careful planning, thorough execution, and continuous monitoring. Seeking support from experienced consultants and leveraging technology can streamline the process.