How to Stay Efficient When Moving Warehouses
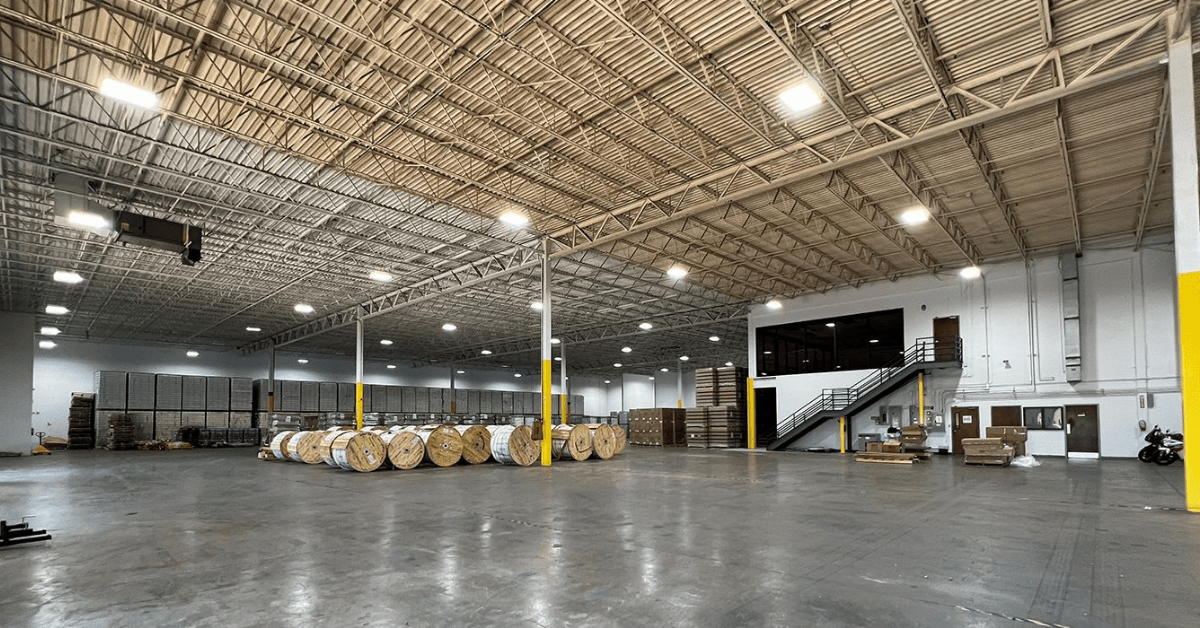
Relocating warehouses is no small undertaking.
Warehouses are central hubs for business activities, ensuring that supply chains stay efficient and inventory moves quickly on and off the shelves. Moving to a new location can take months — or even years — of preparation, and insufficient planning can lead to wasted time, money and energy.
Maximize the efficiency of your move and new space by considering these six factors.
Port Accessibility
Moving to a warehouse conveniently located near a port can help control drayage costs. When calculating the potential overhead costs of a new warehouse location, take the commute into consideration. A space far away from the nearest port may not be as cost-efficient as it initially appears if it results in steep transportation expenses in the long term.
North Carolina offers two deep-water ports in Wilmington and Morehead City in addition to one inland port in Charlotte. The ports boast the highest container truck gate and crane productivity on the East Coast, according to North Carolina State Ports Authority. In recent years, the accessibility of North Carolina’s ports has attracted major distributors such as Walmart and Amazon.
Local Regulations
If opening a warehouse in a different state, consider the local tax structures, incentives and governmental regulations. Stay cost-efficient and prevent last-minute fees by doing your due diligence into the regulations of each possible location.
CNBC and Forbes Magazine have both ranked North Carolina as one of the best states for business because of the low costs and favorable regulatory environment. North Carolina’s corporate tax rate is among the lowest in the country at 2.5 percent.
Organizational Structure
Before you rush into any leases, draft a potential floorplan for the space to ensure you are setting your business up for success. Can the warehouse accommodate both efficient storage and wide aisles? How will inventory move through your space? Ideally, the facility should be able to receive, handle and deliver inventory in a linear fashion.
At this step, some companies choose to partner with a third-party logistics company (3PL) for additional organizational insight. A reputable 3PL has decades of experience in this niche, providing insight into how to maximize the space before moving in materials.
Environmental Factors
Weather can wreak havoc on even the most well-seasoned supply chains, so it should be a key consideration for any interstate warehouse move. Relocating to a state with frequently extreme temperatures may require more preparation than moving to a milder environment.
North Carolina winters are cold but short, and the temperatures are rarely below 20 degrees Fahrenheit. In-state warehousing managers worry less about winter disruptions than other locations along the East Coast, allowing them to stay efficient all year round.
Traffic Density
If your business spends significant time on the road, the costs of traffic can quickly add up. Warehouses in regions with less congestion benefit from shorter transportation times and fewer frustrating driving delays.
Mobile technology firm INRIX found that Raleigh drivers lost only six hours in congestion in 2021, compared to the 62 lost hours that Los Angeles drivers faced. Though the Raleigh region continues to experience high migration rates, local distributors are able to move products more efficiently than comparable port areas around the country.
Future Growth
When planning your warehousing relocation, consider your growth plans. If the company expands as expected, will your warehouse be able to accommodate the increased demand? Will you need more bays to handle more business?
Prepare the warehouse for growth before filling up the space. In the future, your company can quickly and easily scale without the need for intensive reorganization or another relocation.
Armstrong – Raleigh provides commercial relocation, logistics and warehousing services that keep businesses running smoothly. Throughout its rich history, Armstrong has built a reputation for eliminating inefficiencies and exceeding expectations across industries. Get started today by calling 919.425.9853 or requesting a free quote online.