How Construction Companies Are Bolstering Supply-Chain Resilience
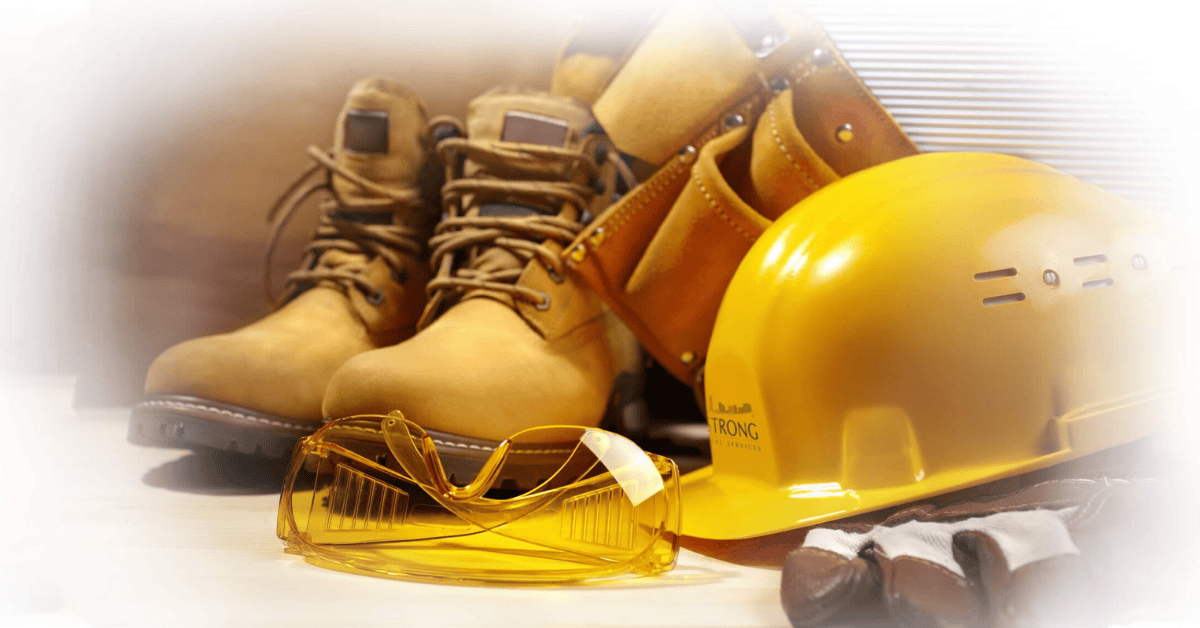
In the face of industry-wide obstacles to the industrial supply chain, construction companies are coming out on top.
During the pandemic, the construction industry has faced unprecedented supply shortages. High demand for lumber, aluminum, steel, cement and paint has made construction materials hard to come by, causing longer lead times and increased costs. NPR reported that lumber prices surged by 333 percent from April 2020 to May 2021 before falling.
Meanwhile, backups at coastal ports have been driving delivery and project delays for construction companies around the U.S. But, despite the supply-chain disruptions, a recent Wells Fargo survey found that the construction industry is optimistic about the future. Construction spending across the country quickly recovered to pre-pandemic levels, peaking at nearly $1.6 trillion in July 2021, according to a Deloitte report.
Additionally, the proposed Build Back Better Act would invest billions into public-infrastructure projects, which construction experts predict could fuel aggressive growth for the industry in 2022. The increased government investment — accompanied by more private-sector spending in 2022 — could further accelerate the construction industry’s recovery.
Industry leaders are taking proactive steps to bolster their supply-chain resilience in preparation for the boom in new business. Here are five ways that growing construction companies are protecting their growth goals from disruptions.
Building up inventory
For decades, construction companies have kept inventories lean by waiting to order raw materials until they have an immediate need. In doing so, they kept overhead costs low but were left unprepared for pandemic-era shortages. Now, construction leaders are keeping more materials and equipment on hand to minimize the effects of global delays and rising prices.
Outsourcing warehousing operations
Instead of attempting to manage all warehousing in-house, executives are turning to third-party logistics partners (3PLs) to store extra materials. A 3PL can provide fully-integrated solutions to smooth out supply chains. Providers with locations on the coast often have easy access to high-traffic ports, allowing them to receive shipments, transport those shipments to the warehouses, sort all materials by SKU and more.
Identifying alternative suppliers
The pandemic has forced companies to look for alternative suppliers outside severely affected areas. Faced with global supply-chain bottlenecks, the construction industry is mitigating risk to projects by searching for sources with different locations and production capacities. Construction companies can strengthen their supply chain by expanding sourcing networks and vetting new partners.
Accessing backup distribution channels
Similarly, construction companies are tapping into new distribution channels to ensure they receive needed materials as soon as possible. Many businesses have chosen to leverage partnerships with third-party logistics providers to keep supply chains moving. Some 3PLs have nationwide networks of owned locations and vetted partners, allowing them to circumvent blocked distribution channels with greater ease.
Recruiting more labor
On top of the supply-chain delays, construction companies are battling a nationwide labor shortage by attempting to recruit more direct labor to accompany contracted work. However, finding qualified candidates to fill open positions can pose significant challenges, so 3PLs are filling the void. Full-service logistics company provide easy access to expert staff who are ready to spring into action.
As the largest asset-based provider of commercial services in the U.S., Armstrong has the services, expertise and assets to keep your business booming amid any circumstances. Armstrong – Raleigh’s dedicated team, real-time asset tracking and convenient access to major ports ensures that your business runs smoothly. Learn more by calling 919.425.9853 or requesting a free quote online.